
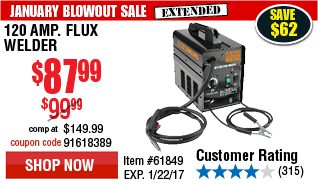

The electrode lead connects the machine to the electrode holder for welding operation while the work lead clamp is connected to the work piece to ensure a safe circuit. Grounding refers to protecting operators and equipment nearby from electrical shock and danger. The circuit needs to be ‘grounded’ in order for the electricity to spark and create an arc upon the workpiece.
#Harbor freight flux welder full
The clamp is an important safety feature to ensure a full electrical circuit that runs through the workpieces and welding machine without shocking the operator. Work Lead Clamp Isn’t Properly ConnectedĪfter making sure that the work lead clamp surface area is clean from any debris, rust, or coating, it also needs to be checked for a proper connection. It is recommended to clean and prep the metal beforehand for best results, both in MIG welding and especially with TIG welding. Not only will coatings on metal potentially prevent a spark, but if you are able to create an arc and weld, it may result in weaker or unattractive weld results.

Heat and paint strippers may also be used, including acetone, but they must be cleared and dry before weld. Sandpaper and angle grinders can be used to strip down to the bare metal. You will want to remove this coating from both the work piece and the clamp connections to ensure a strong electrical circuit. Paints and enamels: These coverings are particularly common when working with automotive work pieces.You can use a wire brush or similar abrasive tool to create a smooth surface. Flaking can also be rust related and should be removed. If this does not work, consider abrasive blasting and then wiping down with acetone or similar solutions. You can try and remove rust with sandpaper or an angle grinder. Rust and corrosion: Rust can be incredibly preventative in creating a spark if on the metal piece.Dirt and debris: Wipe all dirt away from metal pieces before use to ensure a proper connection between the workpiece and clamp area.There are a variety of coatings that could be interfering with this bare metal connection and will need to be removed to prevent inference with arc and welding spark: This means that both the workpiece where you want to form an arc as well as the connection point for the work lead clamp need to be bare metal. One of the most common reasons your welder won’t spark is because the connection points between the welder and the metal pieces are not clean or clear. We’ll start at the top of the list as these are the simplest and work towards internal welder problems that could be resulting in no spark. There are a lot of reasons your welder may not be sparking, but fortunately, most of them are easy fixes. Polarity connections need to be examined.Welding drive roll tension needs adjustment.The work lead clamp is not properly connected.Metal connections areas are not clear or clean.These are the 5 most common reasons why your welder won’t spark: If your welder still won’t spark, there may be problems with the welder itself. If your welder is not sparking, you will first want to look at the welding conditions and environment for the easiest fixes. Why Won’t Your Welder Spark and What to Do 5.Look at Polarity Connection and Configuration.Welding Drive Roll Tension Needs Adjustment Why Won’t Your Welder Spark and What to Do.We will help you identify why your welder may not be sparking and the adjustments you can make to return your welder back into working (and sparking) condition. There are multiple reasons that could be responsible for your welder not sparking, both issues with the connection to the workpiece, or with the welder itself. Examine polarity (negative and positive wire configuration).Adjust wiring connection to and in welder.Make sure metal contact areas are clean.
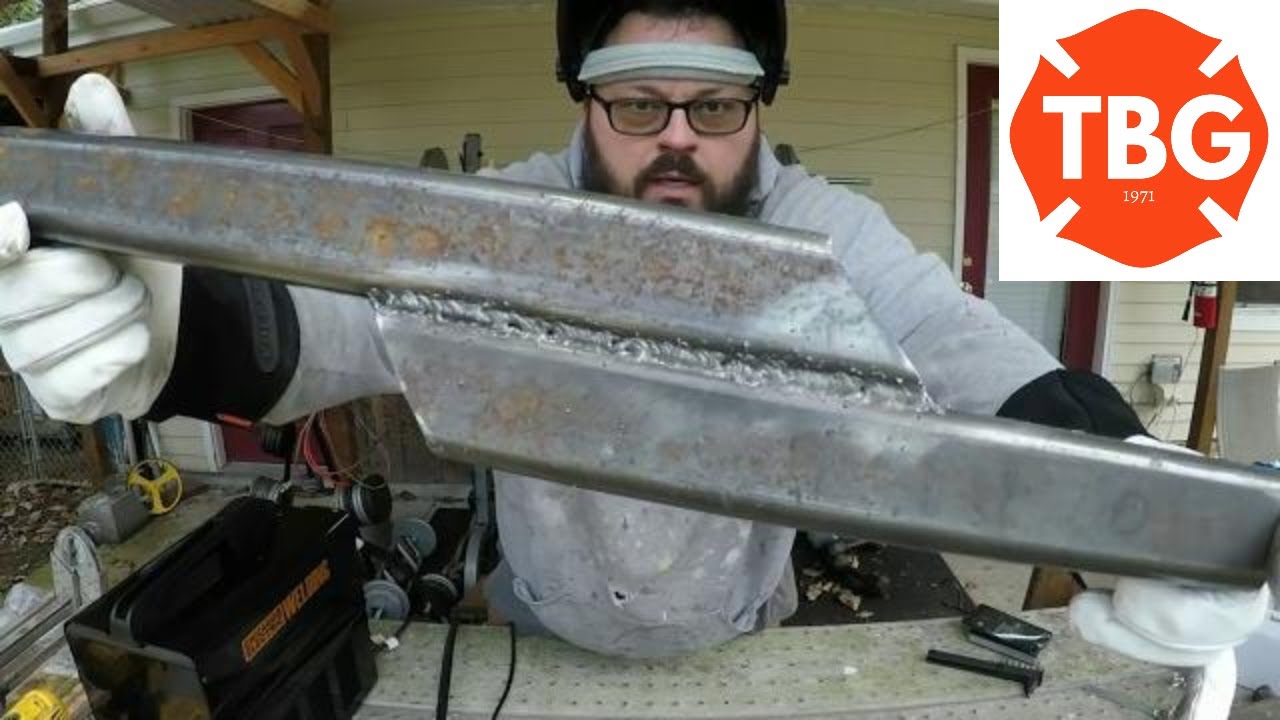
This is what to do when your welder won’t spark: Reason Nr. If these sparks don’t occur, you will not be able to produce clean or stable welds. In the process of arc welding, sparks are created when elements are burned at the electrode or weld puddle at very high temperatures to create your joined seam. Initiating a spark is a key indicator that an electrical arc has formed, and you can successfully join two pieces of metal together.
